-
APPLICATION OF PAINT COAT:
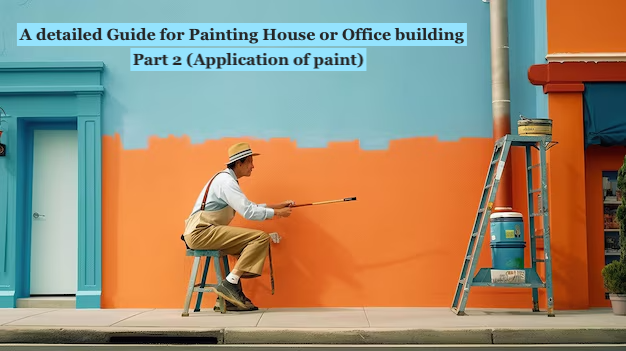
2.1 General
-
The method of application shall be as recommended by the paint manufacturer.
-
Proper tools and implements shall be used. Scaffoldings if used shall be independent of the surface to be painted to avoid shade differences of the freshly repaired anchor holes.
-
Only approved skilled labours shall be employed.
-
All materials shall be evenly applied, so as to be free of sags, runs, crawls or other defects.
-
All coats shall be of proper consistency. In case of application by brush, no brush marks shall be visible. The brushes shall be clean and in good condition before application of paint.
-
All priming undercoats for painting shall be applied by brush only, and rollers, spray equipment etc. shall not be used.
-
Painting work shall not be done under conditions that are unsuitable for production of good results.
-
Painting shall not be done when plastering is in progress or is drying. Application of paint which seals the surface to moisture shall only be done after the moisture on and the base surface has dried out.
-
All coats shall be thoroughly dry before being sand papered or before the succeeding coat is applied.
-
In case the surface is not covered properly by applying the specified number of coats, further coats shall be applied.
-
All primer and undercoats shall be tinted to approximate the colour of the finishing coats. Finished coats shall be of exact colour and shade as per approved samples and all finish shall be uniform in colour and texture. All parts of moldings and ornaments shall be left clean and true to finish.
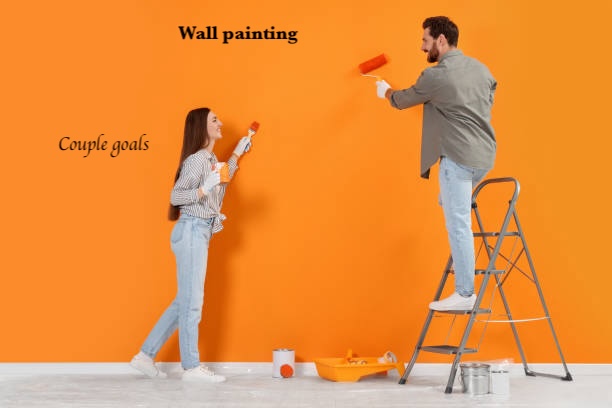
2.2 Application by materials
2.2.1 Synthetic Enamel Paint
Paint shall be applied on properly primed surface. Subsequent coats shall not be applied till the previous coat is dry. The previous coat shall be lightly sand papered for better adhesion of subsequent coats.
2.2.2 Waterproof Cement Paint
Surface to be coated with cement paint shall be washed and brushed down. As soon as the moisture has disappeared, the surface shall be given one coat of paint. Care shall be taken so that the paint does not dry out too rapidly.
After 4 to 6 hours, the water shall be sprinkled over the surface to assist curing and prevent cracking.
After the first coat has dried (24 to 48 hours), the second coat shall be applied in a similar manner.
The finished surface shall be kept moist by occasional sprinkling with water for seven days after painting.
2.2.3 Acrylic Emulsion Paint
Lime gauged cement plastered surfaces shall not be painted for at least one month after plastering. A sample patch shall be painted to check alkali reaction if so desired by the Engineer. Painting shall be strictly as per manufacturer’s specifications.
2.2.4 Oil Bound Distemper
Any unevenness in surface shall be made good by applying putty.
The patched surface shall be allowed to dry thoroughly before the coat of distemper is applied.
One coat of distemper properly diluted with thinner as specified by the manufacturer shall be applied by brushes in horizontal strokes followed immediately by vertical ones, which together will constitute one coat.
Two or more coats of distemper as found necessary shall be applied to obtain even shade.
2.2.5 Flat Oil Paint
Method of application is the same as for oil bound distemper.
2.2.6 Chemical Resistant Fire Resistant and Oil Resistant Paints
In general, methods of application of these paints shall be strictly as per manufacturer’s specifications.
2.2.7 White Washing
The surface where white washing is to be applied shall be cleaned of all loose materials and dirt.
All holes and irregularities of the surface shall be filled up with lime putty and shall be allowed to dry up before application of the lime Solution.
One coat of white wash shall consist of one stroke from top downwards, another from bottom upwards over the first stroke and another from left to right before the previous one dries up.
Second coat shall be applied after the first coat dries up completely and similarly third coat shall be applied and in case the Engineer feels that one or more coats are required the contractor shall do so without any extra costs to the CLIENT.
No brush marks shall show on the finished surface. The inner plastered surfaces of wall shall be given 3 or more coats of white washing.
2.2.8 Colour Washing
For new work, the priming coat shall be of whitewash with lime with whiting.
Two or more coats shall then be applied on the entire, surface till it represents a smooth and uniform finish.
The finished dry surface shall not be powdery and shall not readily come off on hand when rubbed. Indigo (Neel) shall, however, not be added.
2.2.9 Acrylic Copolymer Aggregate Finish
Bonding agent shall be mixed with water. The flakes/granules shall be added and mixed thoroughly and kneaded till no lumps are found.
The dough shall be left for 20-30 minutes before stating application. The bonding agent, flakes/granules and water shall be mixed in different ratios for different finishes as per manufacturer’s specifications.
The first application shall be by steel trowel. Specific finish required shall be applied by plastic trowel after the first applied surface is smoothened.
2.2.10 Plastic Emulsion Paint Finish
Recommendations given by the paint manufacturer shall be strictly followed for mixing and application of paint.
The prepared surface shall be treated with two coats of primer consisting of cement primer, whiting or as per manufacturer’s specifications.
The paint shall be applied with brush or roller. The paint is dried by evaporation of the water content and as soon as the water has evaporated, the next coat can then be applied.
The time of drying varies from 1 hour on absorbed surface and 2-3 hours for non-absorbed surfaces.
The thinning of the emulsion shall be done with water and not by turpentine.
The surface on finishing shall present a flat, velvety smooth finish.
Minimum three coats of Plastic Emulsion paint shall be applied and the colour shade shall be uniform over the area.
2.3 Application by Surface
2.3.1 Masonry, Concrete and Plastered Surface
2.3.1.1 First Primer Coat
It is applied to provide adhesion between the paint film and the surface. It smoothens the surface, makes it less absorbent and increases the spreading capacity of the paint.
2.3.1.2 Application of Putty
This is done to fill the minor cracks and surface imperfections. Drying time for putty is normally 5-6 hrs.
2.3.1.3 Second Primer Coat
This is applied to sandwich putty between two primer coats, since painting directly on putty leads to a patchy appearance.
2.3.1.4 Finish Coat
Generally two coats must be applied to get the desired finish and color. Each coat must be completely dry before the next one is applied. Drying times for different paints vary due to their composition.
2.3.2 Wood Surface
2.3.2.1 Primer Coating
Applied to fill the pores of wood & to provide adhesion between the paint film and the surface.
It smoothen the surface, makes it less absorbent and increases the spreading capacity of the paint. It shall have no turpentine as it impairs the firmness of paint.
Primer shall be either prepared at site or readymade paint of approved brand/manufacturer shall be used.
2.3.2.1.1 First primer coat
After surface preparation and thorough drying of wood, 1st primer coat shall be applied.
2.3.2.1.2 Stopping & filling
After the priming coat is applied, the holes and indentations on the surface shall be stopped with glazier’s putty (1 part white lead + 3 part fine powdered chalk + boiled linseed oil to form stiff paste) or readymade putty of reputed brand.
Stopping shall not be done before the priming coat is applied as the wood will absorb the oil in the stopping and the latter is, therefore liable to crack.
2.3.2.1.3 Second primer coat
This is applied to sandwich putty between two primer coats, since painting directly on putty leads to a patchy appearance.
2.3.2.2 Application of Final Paint
Preparation of Mix
Readymade enamel paint of reputed brand confirming to IS Specification, of desired colour/shade shall only be used.
Paint as supplied shall be used for painting. If required, thinning can be done with mineral turpentine oil to the extent as recommended by manufacturer (max. 5-10%).
Paint coats
Generally one coat should be adequate for old work and two coats (excluding priming coat) for new work to get the desired finish and colour.
In case the earlier paint shade is significantly darker than the new shade, an additional coat of paint is recommended.
Process of Paint application
Paint application shall be carried out with proper painting brush.
Paint shall be applied evenly and smoothly by means of crossing and laying off, the latter in the direction of the grain of wood.
The crossing and laying off consists of covering the area with paint, brushing the surface hard and then brushing alternately in opposite directions, two or three times and finally brushing lightly in a direction at right angles to the grains.
In this process, no brush marks shall be left after the laying off is finished. The full process of crossing and laying off will constitute one coat.
The subsequent coats shall be applied only after the previous coat has dried. Before application of next coat, previous coat shall be lightly rubbed down with sandpaper and dust shall be cleaned.
The finish surface shall be even and uniform and shall have no brush marks.
-
CLEANING UP
Upon completion of painting etc. remove all marks and make good surfaces, where paint has been spilled, splashed or splattered. Including all equipment, Fixtures, glass furniture, fittings, site to the satisfaction of the Engineer-in-Charge.
-
ACCEPTANCE CRITERIA
All painted surfaces shall be uniform and pleasing in appearance. The color, texture, etc. shall match exactly with approved samples. All stains, splashes and splatters of paints shall be removed from surrounding surfaces.
-
STORAGE & HANDLING OF MATERIALS
- Paints being inflammable material should be protected against fire hazards by
a) Providing fire extinguishers and sand buckets at easily accessible places.
b) Applying fire retardant paint on walls of store room.
c) Keeping away fire prone materials such as wood, cotton waste etc.
d) Displaying ‘No Smoking’ Boards at all important locations.
Other precautions:
- Electrical short circuiting should be avoided in paint stores by way of providing concealed(Electrical) wiring.
- Proper ventilation arrangements should be provided where paints are stored.
- Water should not be used to extinguish the fire.